
[ad_1]
“We’ve got just enough.”
Sleiman’s local business has been overrun with project requests this year, but his crew at Apex Concrete and Landscaping is having a major issue: finding enough concrete.
Apex used to schedule concrete trucks based on the projects they had coming up. Now, they’re booking any available concrete and trying to squeeze clients into those days. Some jobs are being pushed back weeks as they wait for materials and other Calgary companies, like Omega 2000 Cribbing Inc., are turning clients away.
“I don’t know how other contractors are going to survive. I don’t know how the suppliers [are] going to keep providing,” said Sleiman.
The construction sector is having a boom year, as consumers and companies pour more dollars into building infrastructure. But cement, a key ingredient in making concrete, has become scarce, and the shortage — caused by a confluence of increased demand, labour shortages, inflation and issues at major plants — is creating serious problems for the construction industry across the country.
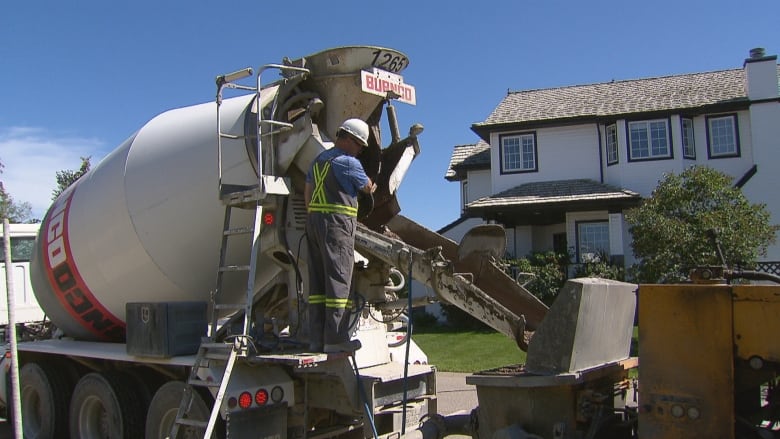
Increased demand, shrunken workforce
One undisputed cause of the shortage is an increase in demand. “This is a good-weather summer. And people have put off building for a while, and the money has come from governments.… And now everybody wants to do everything all at once,” Michael Veall, a professor of economics at McMaster University, said.
“It’s not surprising that the economy takes a little time to get adjusted to this new level of rapid construction growth.”
There are many reasons why supply is struggling to keep up with demand. BURNCO, a North American ready-mix concrete producer, says it’s experiencing issues with supply chains (particularly with machinery, repairs, and maintenance) and global constraints limiting the amount of raw materials available to make cement. Canada imported about $895 million in cement and concrete-related goods in 2021, according to Industry Canada, mostly from the U.S. and China.
“The shortages appear to be persistent through year-end at minimum,” Tom Zais, the CEO of BURNCO, told CBC News.
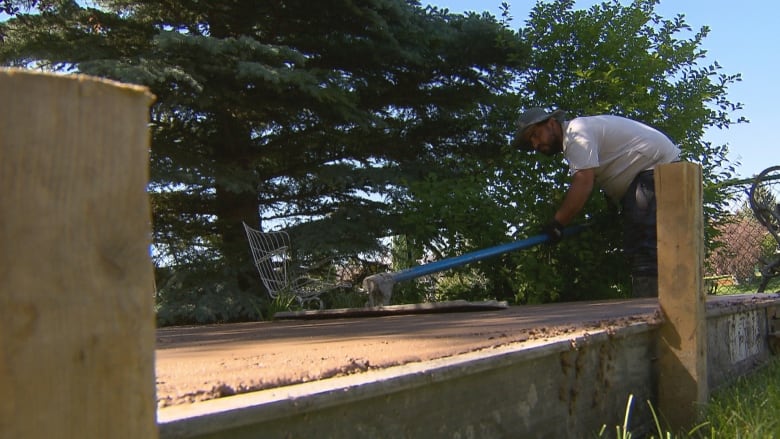
That growing demand is also being exacerbated by a shrinking workforce — which was an industry issue even before the pandemic started.
“We were already forecasting that there would be a likely shortage of workers, primarily because the baby boomers make up such a significant proportion of our workforce,” said Mary Van Buren, the president of the Canadian Construction Association, explaining that those retirements and the pandemic have devastated the work force.
Inflation is also a factor. Prices for many raw construction materials have risen over the last 12 months. Costs for categories like gravel and clay have also risen, up eight per cent since last summer, according to Statistics Canada’s raw materials price index. In April 2022, the National Association of Home Builders in the U.S. released numbers showing that ready-mix concrete is nine per cent more expensive than it was at the start of 2021. The association also found building material prices for items like lumber, paint and concrete, have risen more than 30 per cent since the start of the COVID-19 pandemic.
Sleiman says that Apex is spending about 30 per cent more on its concrete than it did last year.
Problems at major plants are yet another piece of the crisis. In May, one of B.C.’s largest cement plants, the Lafarge facility in Richmond, caught fire. Production was cut as a result.
Also in May, a five-week concrete workers’ strike on the Lower Mainland shut down 12 facilities operated by three companies, and at one point impacted half of construction projects in Metro Vancouver and the Fraser Valley. That action concluded at the end of June.
“It was going to show some cracks somewhere”
People in the industry are looking for ways to alleviate the pressure. A longer-term vision for infrastructure plans across the country, enabling skilled immigrants to move to Canada and facilitating students to be trained in trades, are all ways to move forward, Van Buren said.
In the meantime, Veall says it may just be a case of waiting for the market to follow its natural cycle and calm down.
“We’ve had a very sharp burst of demand over the last six months, and it was going to show some cracks somewhere.”
On the ground, the Ready Mixed Concrete Association of Ontario has called it a period of “unprecedented challenges” to get the supplies to produce concrete this year, and Toronto-based St Marys Cement announced at the end of June that it was temporarily suspending sales in most of Ontario, and could not deliver any cement from three facilities for an entire week because of the issues.
The materials shortage affecting concrete is expected to last until December at the very least, according to industry forecasts. And that prolonged uncertainty for the rest of construction season is leading to tough choices for businesses like Sleiman’s.
“What am I going to do,” he asked. “Half a job?”
[ad_2]
التعليقات